Yes, we all want to get the best value out of our mines. Typically, we aim to produce an optimal schedule where the blasting is well executed, the mine fleet is effectively utilized, the ore feed is on target and the volume of stockpile material is sufficient to meet the right blend for each product.
All these aspects are important, but shouldn’t we start by making sure that not only our schedule, but also our final saleable product blend is optimal? If we do, this can add more value into our mining operations.
But the reality is that for many mines this is not a straightforward task. This is why I’d like to share some ideas on how you can achieve this in a fairly simple way.
Optimizing your final product blend is an effective way to increase the value of your mine.
Product Requirements
First things first: Let’s look at some typical product requirements in the mining industry.
Thermal coal operations can usually sell a range of products with different qualities (e.g. ash and energy contents), with each product receiving a different price.
Iron ore operations can have a range of products that are defined by market contracts regarding phosphorus, silica, alumina and LOI levels, as well as a minimum iron grade. Iron ore contracts can also have penalties associated with deviations of contaminating elements from product specification.
To meet the requirements of these types of operations, we really need to make sure that planning the extraction of our reserves will consider all the possibilities to give us the highest NPV we can get. The question for a lot of mine planners is how to accomplish this.
Multiple Products vs. One Final Product
One method that I have found successful is to construct a plan not just with a single final product, but taking into account that a block can be blended with other blocks to make one of many alternative final products.
I can either sell a higher quantity of a lower quality product for a lower price, or sell a lower quantity of a higher quality product for a higher price. Those options, together with other variations, immediately lend themselves to an optimization approach.
Each product we produce in the plant will have its own specifications, its own blend and its own value or sales price. This ensures that blending constraints are met and penalties are applied to the final products.
I remember helping some of our iron ore clients with the following problem: they struggled to control the blend (and therefore the penalties) caused by high phosphorus in their product.
So we came up with a solution where they could control these penalties. Instead of having one product, we made a plan that had multiple products, each with a defined phosphorus range, and then we adjusted the prices to compensate for the phosphorus penalty. This meant that each product had a unique price to account for penalties.
The next step was to determine how to model this using strategic mine planning software.
Modelling Alternative Products
We used Minemax Scheduler to model alternative products. First we defined multiple products, each with its own range for grade (Fe) and contaminants (P). Then we gave each product a unique price to account for the penalties it incurs due to the level of contaminants. We also set the mining costs for each blend as well as constraints for grade and contaminants in the model. Finally, we ran the optimization to calculate the best schedule with the optimal product blend for the operation.
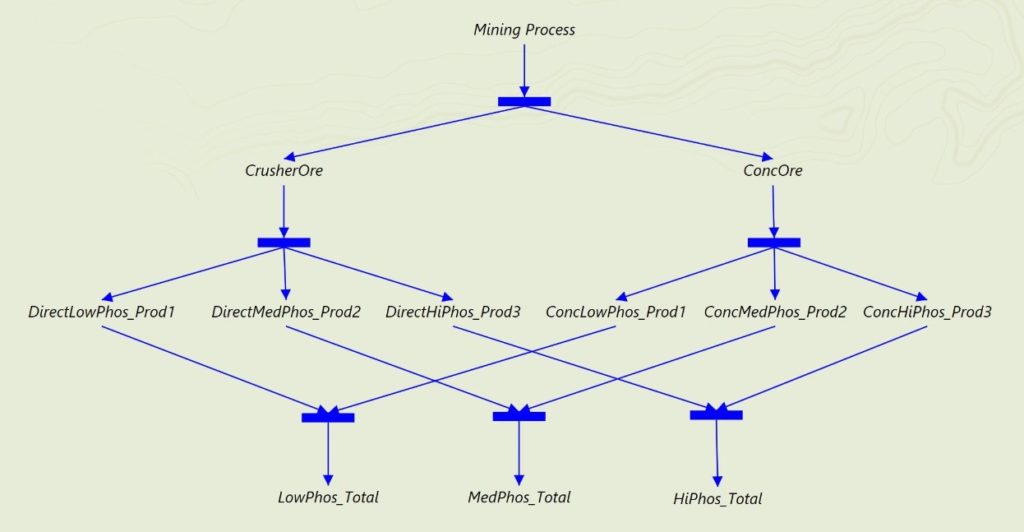
Results
The results of this approach were an eye opener . They showed me how easy it can be to deliver a more consistent product blend and realize a greater NPV just by adding more detail into our mine schedule. The optimization of the multiple products model gave a significantly higher NPV as compared to the single product model.
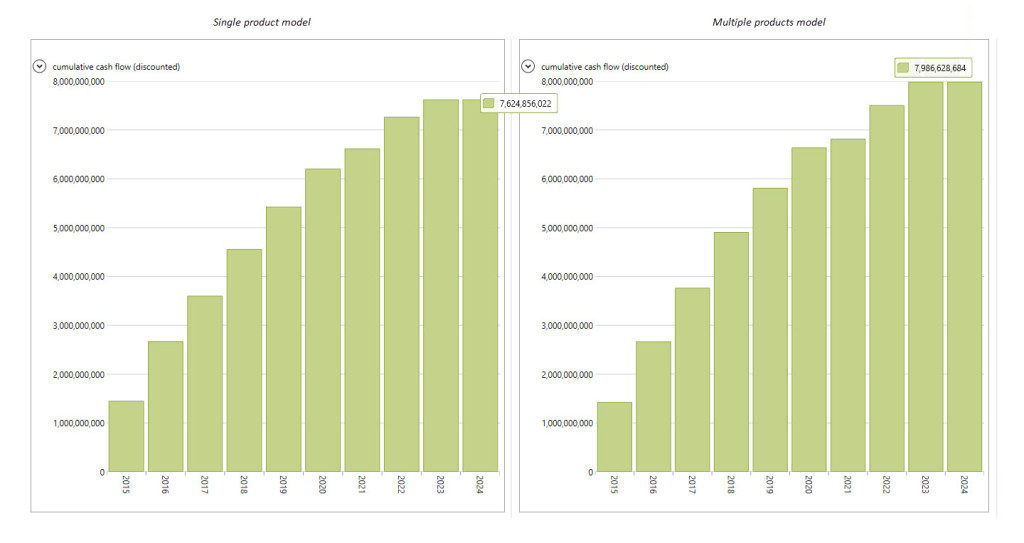
What’s more, the erratic trend in the grade for each product has become more consistent throughout the schedule.
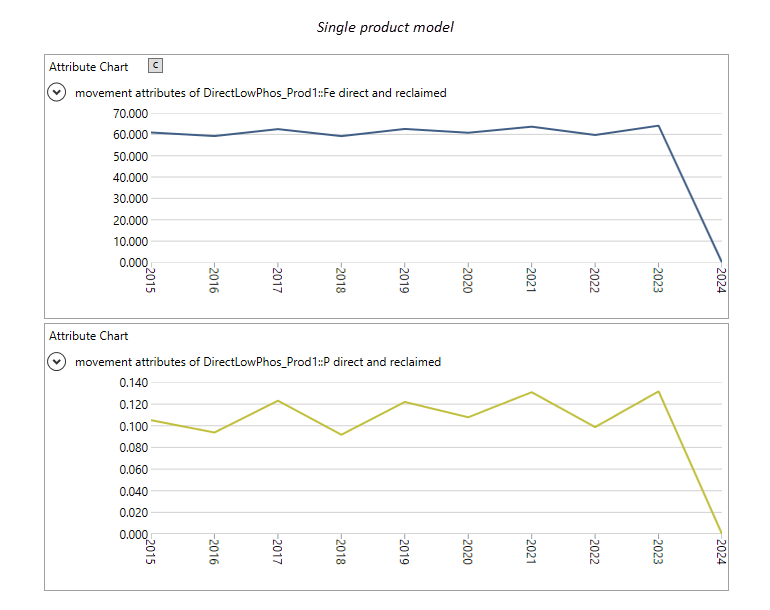
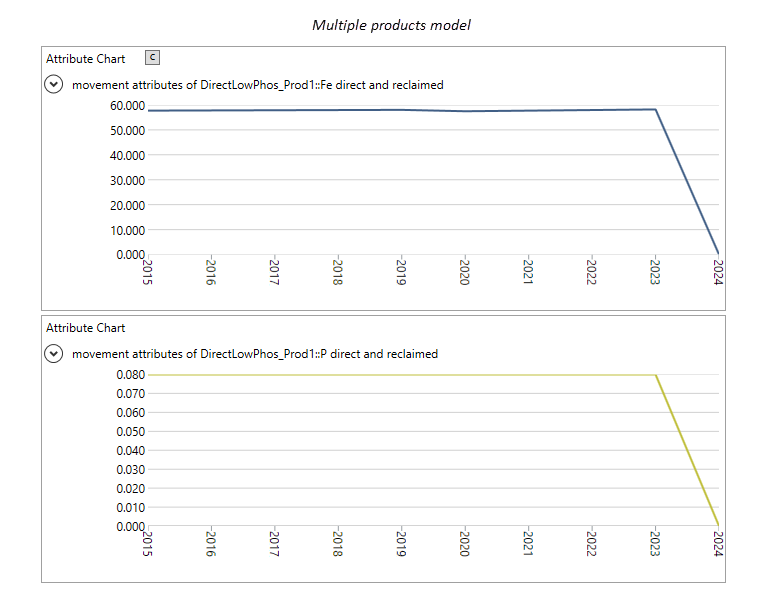
Summary
I have shown you one example where we have used an alternative products modelling approach to achieve a schedule with a higher NPV than when we used a single product in the model.
When you model multiple products with specific blend ranges and associated penalties, you can be confident that you are getting the best value out of your project. When the market has demand for a particular blend of product, and you have the operational capacity to manage the production of multiple products, then you can develop a mine plan to meet that demand.
Yes, the selling price plays a big part in determining the value of your mine. However, when you are able to also consider the grades and contaminant levels of your ore, you can calculate how to produce the most profitable product blend, the one that will yield the best value for your operation.
If you want to know more about this, please feel free to contact me and I will gladly discuss this approach with you.